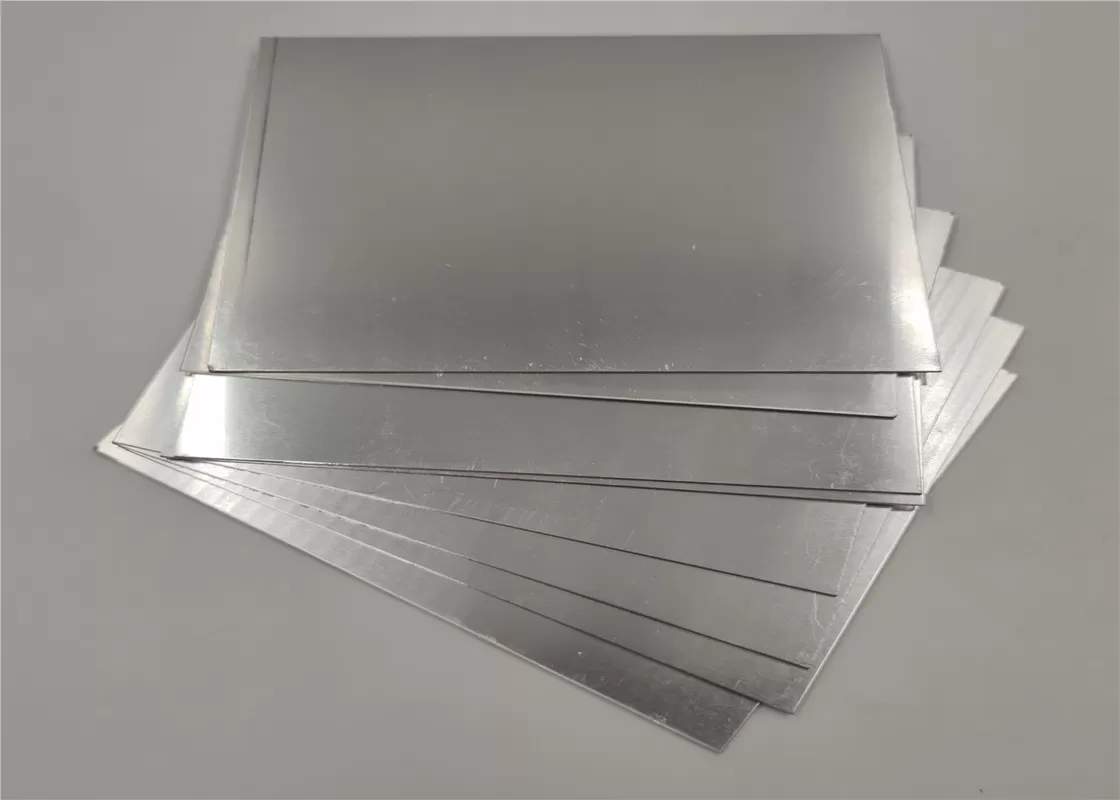
6061 Aluminum Plate
- Product: Aluminum Sheet/Plate
- Alloy: 1050, 1060, 1100, 1070, 3003, 3004, 3105, 5052, 5754, 5083, 6061, 6063, 6062, 7075, 8011
- Temper: H12, H14, H16, H24, H26, H32, O, H112, T3, T6, T4, T651, etc.
- Surface: Mill finish, color coated, embossed, engraving, checkered
- Thickness: 0.2-200mm
- Width:10-2600mm
Description
6061 aluminum plate is a versatile, heat-treatable alloy known for its outstanding strength, corrosion resistance, weldability, and machinability. With a good strength-to-weight ratio, it is easily formed, machined, and welded. Our plate is available in a variety of tempers, including T4, T6, and T651, each with unique mechanical properties for different applications. 6061 alloy is particularly popular in the aerospace, automotive, construction, and consumer goods industries, where it is used to manufacture components such as aircraft skins, automotive parts, building frames, and more. Choose our 6061 aluminum plate, a material that combines durability and ease of use, backed by our mill expertise and global supply capabilities.
| 6061 Aluminum Plate Parameters
Product | 6061 Aluminum Plate |
Temper | H12,H14,H16,H24,H26,H32,O,H112,T3,T6,T4,T651,ect. |
Surface | Mill finish, color coated, embossed, engraving, checkered |
Thickness | 0.2-200mm, or customize |
Width | 10-2,600mm, or customize |
Length | 100-100,000mm, or customize |
Packing | Standard export packaging options include wooden boxes, or as specified |
Payment | T/T, L/C 100% at sight |
MOQ | Normally 5 tons, special require need discuss |
Delivery time | 1-3 days for spot goods, 10-15 days for normal size, 15-25 days for special size |
| Chemical Composition of 6061 Aluminum Plate
Element | AI | Mg | Mn | Si | Fe | Cu | Zn | Cr | Other | |
6061 | Each | Total | ||||||||
Remainder | 0.8 – 1.2% | 0.15% | 0.4 – 0.8% | 0.70% | 0.15 – 0.4% | 0.25% | 0.04 – 0.35% | 0.05% | 0.15% |
| Advantages of 6061 Aluminum Plate
- High Strength-to-Weight Ratio: 6061 alloy is known for its excellent strength relative to its weight, making it ideal for applications where weight savings are important.
- Good Corrosion Resistance: The alloy has natural resistance to corrosion, which can be further improved through various surface treatments.
- Excellent Weldability: 6061 aluminum plate is easy to weld, allowing for strong and stable welds, which is beneficial for fabrication processes.
- Heat Treatable: The 6061 alloy can be heat treated, which enhances its mechanical properties, such as tensile strength and yield strength.
- Good Machinability: It is relatively easy to machine, allowing for precise fabrication and the creation of complex parts.
- Formability: The alloy can be easily formed into various shapes through processes like bending, stamping, and extrusion.
- Aesthetic Appeal: The mill finish provides a clean, uniform appearance that is suitable for both functional and aesthetic applications.
- Non-Magnetic: As with other aluminum alloys, 6061 is non-magnetic, which is an advantage for applications where magnetic interference is undesirable.
- Non-Toxic: Being non-toxic, it is safe for use in applications that may come into contact with food or beverages.
- Recyclability: The material is fully recyclable, contributing to environmental sustainability.
- Thermal Conductivity: It has good thermal conductivity, which can be useful in applications where heat dissipation is necessary.
- Cost-Effectiveness: 6061 aluminum plate offers a good balance of properties at a competitive cost.
| Why Choose Us
- Innovative Custom Formulations: We don’t just offer standard aluminum products; we specialize in developing custom aluminum alloys tailored to specific industry needs, providing a solution that no other supplier can match.
- Sustainability Leadership: Our production processes are designed with sustainability in mind, from energy-efficient manufacturing to the use of recycled materials, positioning us as an industry leader in eco-friendly aluminum products.
- Exclusive Technology: We utilize proprietary technology that enhances the properties of our aluminum products, such as increased strength-to-weight ratios or unique surface treatments that offer superior resistance to environmental factors.
- Expert Consultation: Our team of experts provides unparalleled consultation services, working closely with customers to understand their unique challenges and offering tailored solutions that are unmatched in the market.
- Integrated Supply Chain Solutions: We offer a seamless, integrated supply chain solution that includes everything from raw material sourcing to finished product delivery, ensuring a level of convenience and efficiency that is unique in the industry.
- Advanced R&D Capabilities: With a state-of-the-art research and development facility, we are at the forefront of aluminum technology, constantly pushing the boundaries of what’s possible with our materials.
- Patented Processes: We have patented processes that give our aluminum products a distinct edge in terms of quality, performance, and applications, which cannot be replicated by competitors.
- Strategic Global Partnerships: Our strategic partnerships with key industry players provide customers with access to a network of resources and expertise that is unique to our company.
- Guaranteed Performance: We offer a performance guarantee on our aluminum products, ensuring customers that our materials will meet or exceed their expectations in real-world applications.
- Cultural Alignment and Ethical Practices: Our company operates with a strong ethical code and a culture that aligns with our customers’ values, building trust and a partnership that goes beyond mere transactions.
- Post-Sale Support and Education: We provide ongoing support and educational resources to help customers maximize the performance of our aluminum products, ensuring they get the most value from their investment.
- Exclusive Access to Niche Markets: We have established channels into niche markets that other suppliers cannot access, offering our customers unique opportunities for growth and expansion.
| process flow diagram
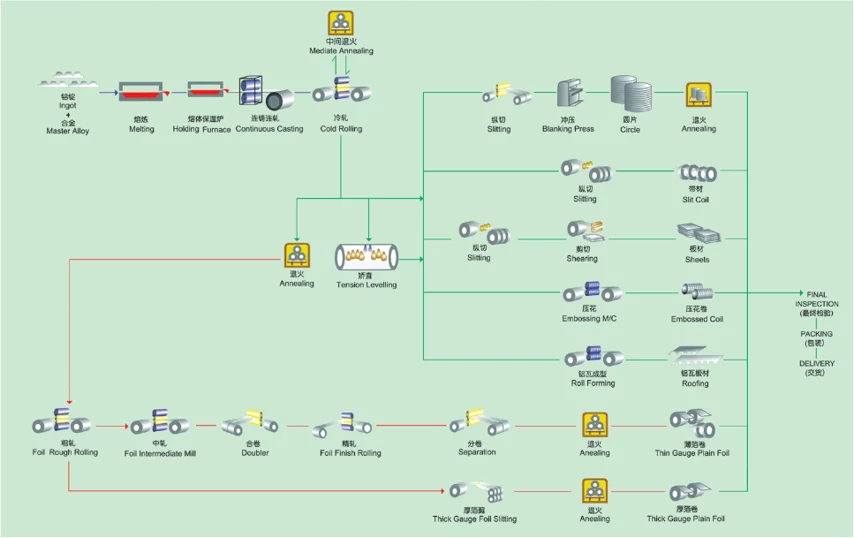
| 8011 Mill Finish Aluminum Plate Production Flow Chart
Hot-rolling
Smelting–standing–casting–fire–hot-rolling–cold-rolling –finished product annealing-packing
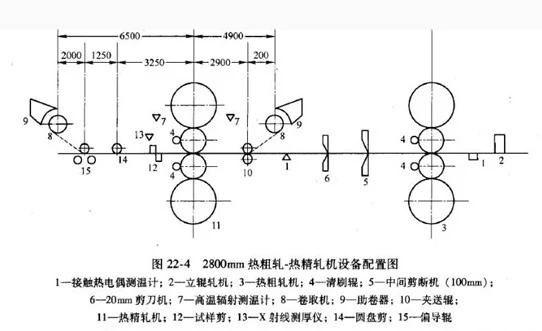
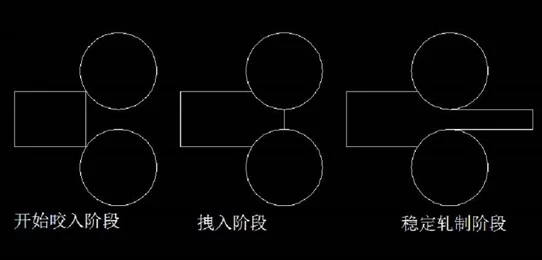
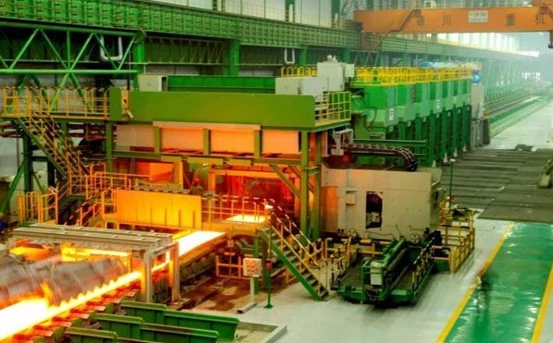
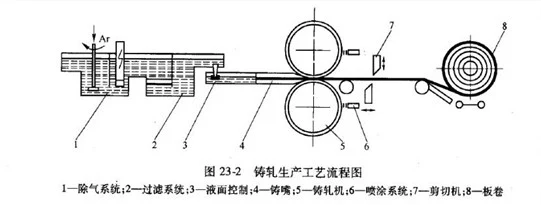
Cast-rolling
Smelting– standing — cast-rolling– cold-rolling– finished product annealing– packing
Casting
The purpose is to manufacture casting components that meet the requirements for a high purity alloy melt and create favorable conditions for casting various shapes.
Several key parameters in the casting process include:
- During the casting process, workers need to continuously add Al-Ti-B wire to refine the grain.
- The temperature generally needs to be set at 1050°C when smelting, with the material’s temperature under constant monitoring, and the metal temperature should be controlled to be less than 770°C.
- At around 735°C, workers need to perform slag operations; this temperature is favorable for the separation of slag from the liquid.
- Generally, two refining processes are required: one using a solid refining agent and the other using a gas refining method.
- After approximately 30 minutes to 1 hour of inert gas purging, workers need to cast in a timely manner; otherwise, re-refining may be necessary.
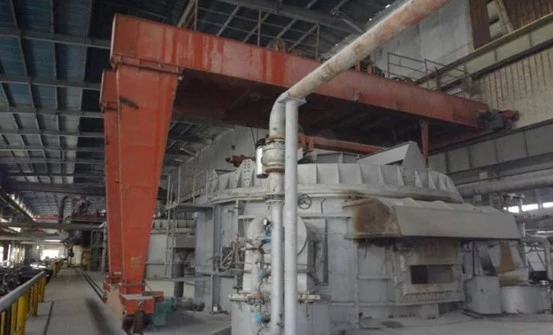
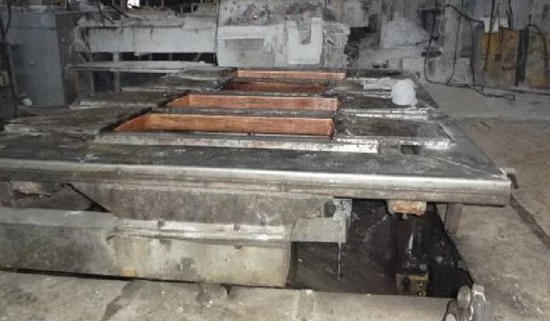
Tension Lever
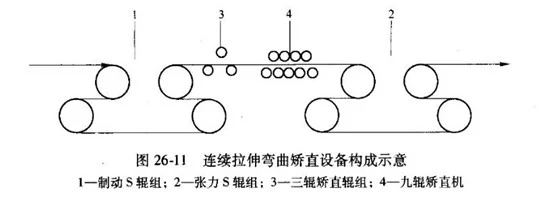
Slitting Mill
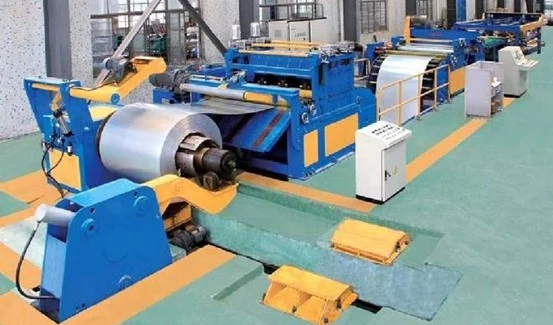
Cross Cutting Mill
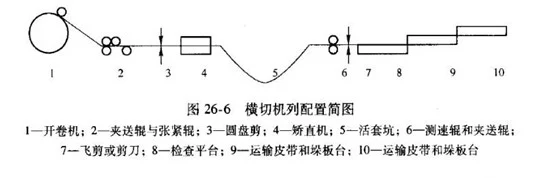
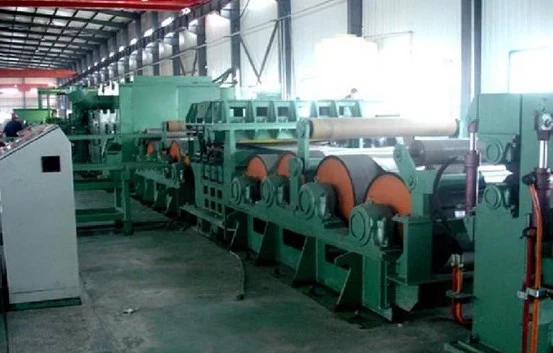
Packing
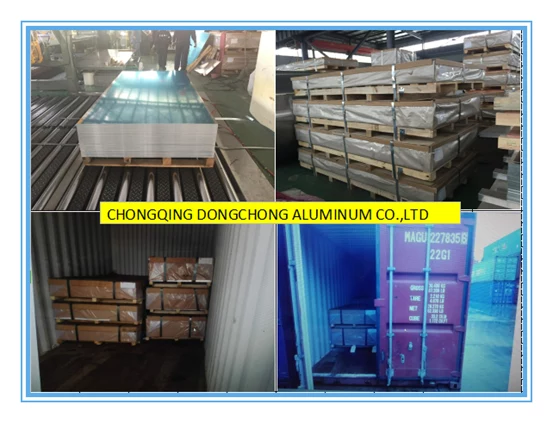
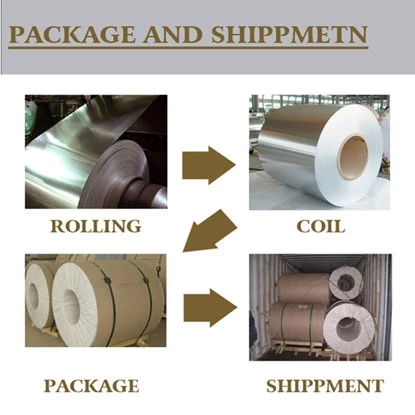