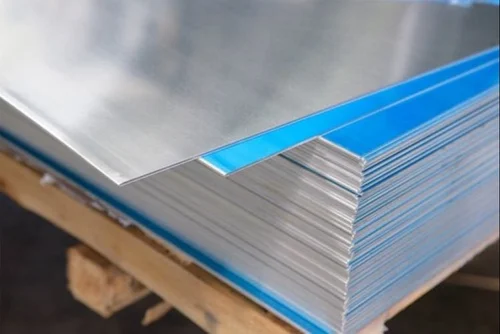
5083 Aluminum Plate
- Product: Aluminum Sheet/Plate
- Alloy: 1050, 1060, 1100, 1070, 3003, 3004, 3105, 5052, 5754, 5083, 6061, 6063, 6062, 7075, 8011
- Temper: H12, H14, H16, H24, H26, H32, O, H112, T3, T6, T4, T651, etc.
- Surface: Mill finish, color coated, embossed, engraving, checkered
- Thickness: 0.2-200mm
- Width:10-2600mm
Description
5083 aluminum plate is a non-heat-treatable alloy known for its excellent corrosion resistance, good cold forming, welding and spot welding properties, and moderate strength. Commonly used in the marine, automotive and aerospace industries, 5083 aluminum plate is also suitable for storage tanks, TV towers and various plate metal parts. With tensile strengths ranging from 160 to 230 MPa and elongation up to 23%, our sheets offer the perfect balance of strength and machinability to meet your manufacturing needs. Choose our 5083 aluminum plate, which is a material that combines durability and ease of use, backed by our factory expertise and global supply capabilities.
| 5083 Aluminum Plate Parameters
Product | 5083 Aluminum Plate |
Temper | H12, H14, H16, H24, H26, H32, O, H112, T3, T6, T4, T651, ect. |
Surface | Mill finish, color coated, embossed, engraving, checkered |
Thickness | 0.2-200mm, or customize |
Width | 10-2,600mm, or customize |
Length | 100-100,000mm, or customize |
Packing | Standard export packaging options include wooden boxes, or as specified |
Payment | T/T, L/C 100% at sight |
MOQ | Normally 5 tons, special require need discuss |
Delivery time | 1-3 days for spot goods, 10-15 days for normal size, 15-25 days for special size |
| Chemical Composition of 5083 Aluminum Plate
Aolly | AI | Mg | Mn | Si | Fe | Cu | Zn | Other | |
5083 | Each | Total | |||||||
Remainder | 4.0 – 4.9% | 0.15 – 0.40% | ≤ 0.10% | 0.20% | 0.10% | 0.10% | 0.05% | 0.15% |
| Advantages of 5083 Aluminum Plate
- Superior Corrosion Resistance: The 5083 alloy is renowned for its exceptional resistance to corrosion, especially in marine and coastal environments.
- Weldability: It is highly weldable, allowing for strong and stable welds, which is crucial for applications that require joining materials together.
- Formability: The plate can be easily formed and shaped, making it suitable for complex design requirements and fabrication processes.
- Strength: With a good balance of strength and ductility, 5083 alloy provides structural integrity in applications that require moderate strength.
- Aesthetic Appeal: The mill finish offers a uniform, matte surface that is visually appealing for applications where appearance is important.
- Non-Magnetic: Being non-magnetic, it is beneficial for applications where magnetic interference is a concern.
- Non-Toxic: It is safe for use in applications that may come into contact with food or beverages.
- Recyclability: As with all aluminum products, 5083 mill finish plates are fully recyclable, contributing to environmental sustainability.
- Cost-Effectiveness: The alloy is a cost-effective choice, offering a good balance of properties at a competitive price.
- Thermal Conductivity: It has good thermal conductivity, which can be advantageous for applications requiring heat dissipation.
| Why Choose Us
- Innovative Custom Formulations: We don’t just offer standard aluminum products; we specialize in developing custom aluminum alloys tailored to specific industry needs, providing a solution that no other supplier can match.
- Sustainability Leadership: Our production processes are designed with sustainability in mind, from energy-efficient manufacturing to the use of recycled materials, positioning us as an industry leader in eco-friendly aluminum products.
- Exclusive Technology: We utilize proprietary technology that enhances the properties of our aluminum products, such as increased strength-to-weight ratios or unique surface treatments that offer superior resistance to environmental factors.
- Expert Consultation: Our team of experts provides unparalleled consultation services, working closely with customers to understand their unique challenges and offering tailored solutions that are unmatched in the market.
- Integrated Supply Chain Solutions: We offer a seamless, integrated supply chain solution that includes everything from raw material sourcing to finished product delivery, ensuring a level of convenience and efficiency that is unique in the industry.
- Advanced R&D Capabilities: With a state-of-the-art research and development facility, we are at the forefront of aluminum technology, constantly pushing the boundaries of what’s possible with our materials.
- Patented Processes: We have patented processes that give our aluminum products a distinct edge in terms of quality, performance, and applications, which cannot be replicated by competitors.
- Strategic Global Partnerships: Our strategic partnerships with key industry players provide customers with access to a network of resources and expertise that is unique to our company.
- Guaranteed Performance: We offer a performance guarantee on our aluminum products, ensuring customers that our materials will meet or exceed their expectations in real-world applications.
- Cultural Alignment and Ethical Practices: Our company operates with a strong ethical code and a culture that aligns with our customers’ values, building trust and a partnership that goes beyond mere transactions.
- Post-Sale Support and Education: We provide ongoing support and educational resources to help customers maximize the performance of our aluminum products, ensuring they get the most value from their investment.
- Exclusive Access to Niche Markets: We have established channels into niche markets that other suppliers cannot access, offering our customers unique opportunities for growth and expansion.
| process flow diagram
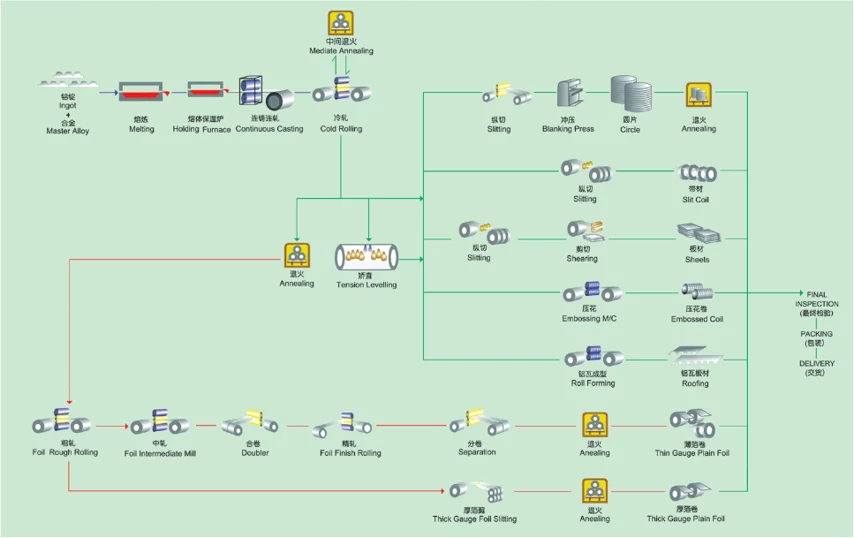
| 8011 Mill Finish Aluminum Plate Production Flow Chart
Hot-rolling
Smelting–standing–casting–fire–hot-rolling–cold-rolling –finished product annealing-packing
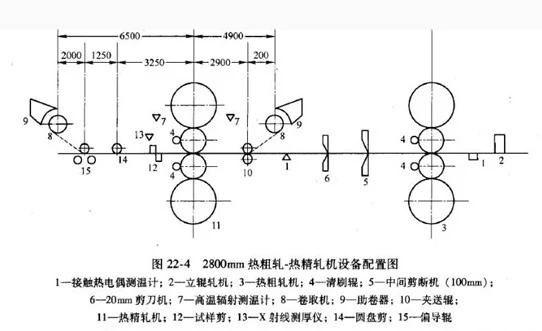
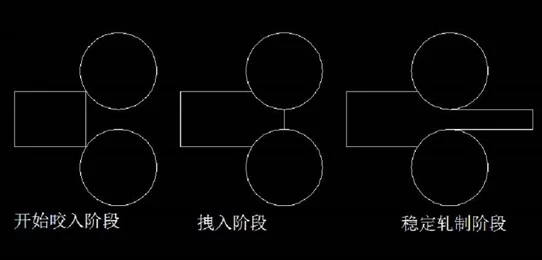
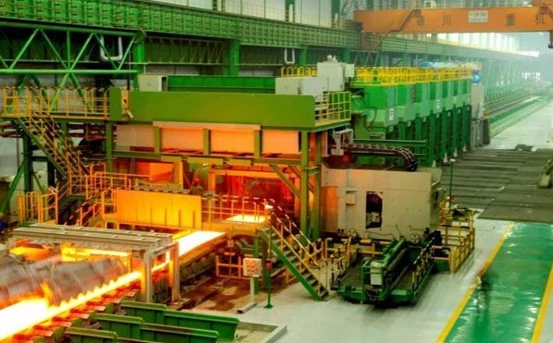
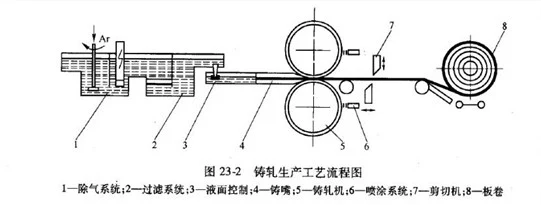
Cast-rolling
Smelting– standing — cast-rolling– cold-rolling– finished product annealing– packing
Casting
The purpose is to manufacture casting components that meet the requirements for a high purity alloy melt and create favorable conditions for casting various shapes.
Several key parameters in the casting process include:
- During the casting process, workers need to continuously add Al-Ti-B wire to refine the grain.
- The temperature generally needs to be set at 1050°C when smelting, with the material’s temperature under constant monitoring, and the metal temperature should be controlled to be less than 770°C.
- At around 735°C, workers need to perform slag operations; this temperature is favorable for the separation of slag from the liquid.
- Generally, two refining processes are required: one using a solid refining agent and the other using a gas refining method.
- After approximately 30 minutes to 1 hour of inert gas purging, workers need to cast in a timely manner; otherwise, re-refining may be necessary.
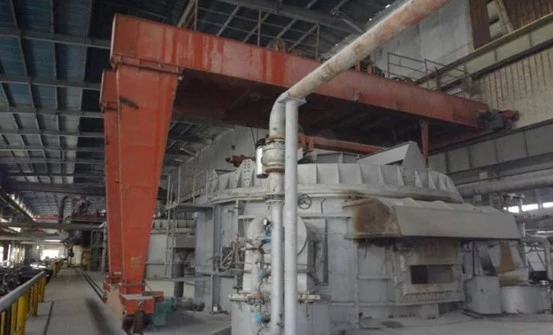
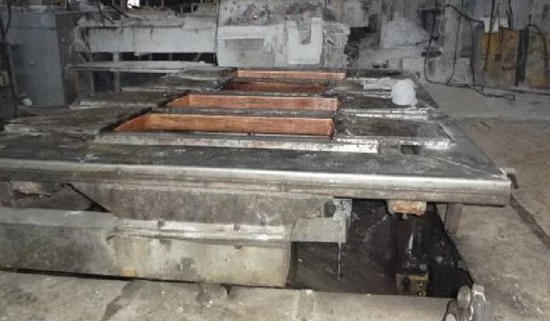
Tension Lever
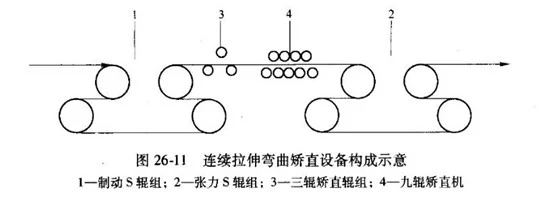
Slitting Mill
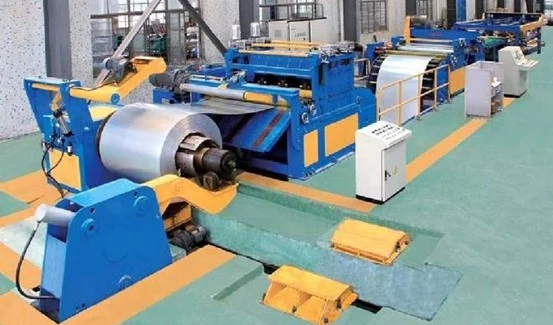
Cross Cutting Mill
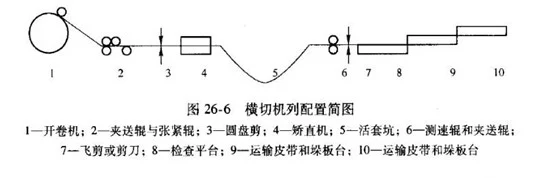
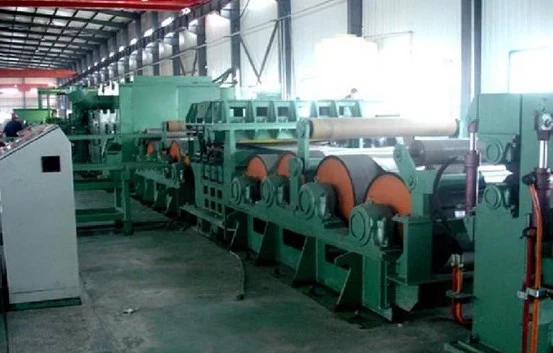
Packing
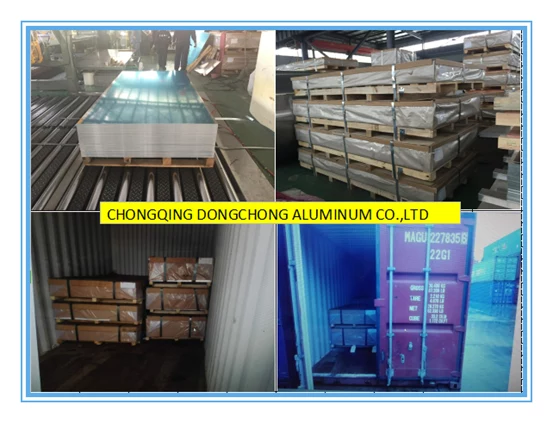
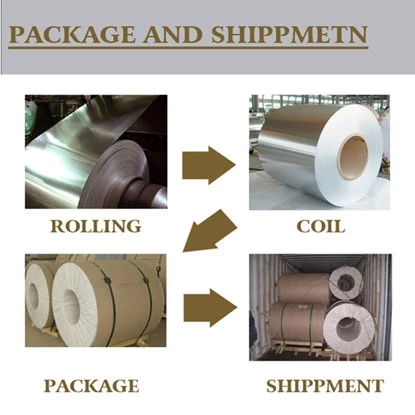